What Is Plastic Fabrication?
Plastic fabrication is the process of using various techniques to convert raw plastic materials into finished goods, from basic household items to complex components for niche industries. As a fundamental aspect of contemporary manufacturing, it plays a key role in producing durable, adaptable products that fuel innovation across a wide range of applications.
Through advanced methods, plastic fabrication companies shape and refine plastics to meet specific design and functional requirements. This process not only supports industries like automotive, medical, and electronics but also addresses evolving environmental considerations in sustainable manufacturing practices.
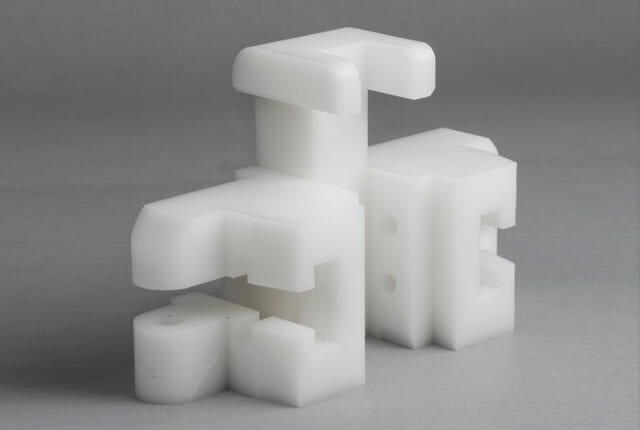
I. Basics of Plastic Fabrication:
1.1 Definition and Overview:
Plastic fabrication involves the manipulation and transformation of plastic materials to create a diverse array of products. Plastics, derived from polymers, can be molded, extruded, or machined to achieve desired shapes and properties. The processes involved in plastic fabrication allow for customization, precision, and scalability, making it a preferred method in many industries.
1.2 Types of Plastics Used in Fabrication:
Various types of plastics are employed in fabrication, each possessing unique characteristics that influence their applications. Common plastic types include polyethylene, polypropylene, polystyrene, polyvinyl chloride (PVC), and more. The choice of material depends on factors such as strength, flexibility, heat resistance, and intended application.
II. Plastic Fabrication Processes:
2.1 CNC Machining
Computer Numerical Control (CNC) machining is a subtractive process that involves cutting, milling, or drilling plastic materials using computer-controlled machinery. This precise method is suitable for producing prototypes, intricate components, and custom-designed parts.
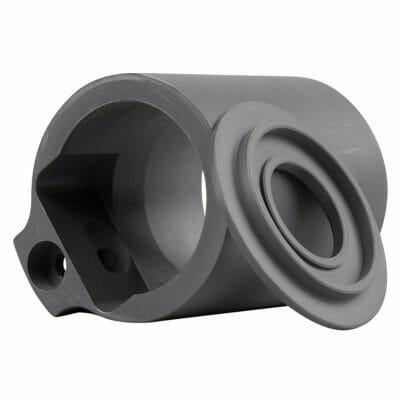
2.2 Welding and Bonding:
Welding and bonding are fabrication processes that join plastic components together. Techniques such as ultrasonic welding, solvent bonding, and adhesive bonding are employed to create strong and durable connections between plastic parts.
2.3 Injection Molding:
Injection molding is a widely used plastic fabrication process. It involves injecting molten plastic material into a mold cavity, where it cools and solidifies to take the shape of the mold. This method is highly efficient for the mass production of complex and intricate parts with high precision.
2.4 Blow Molding:
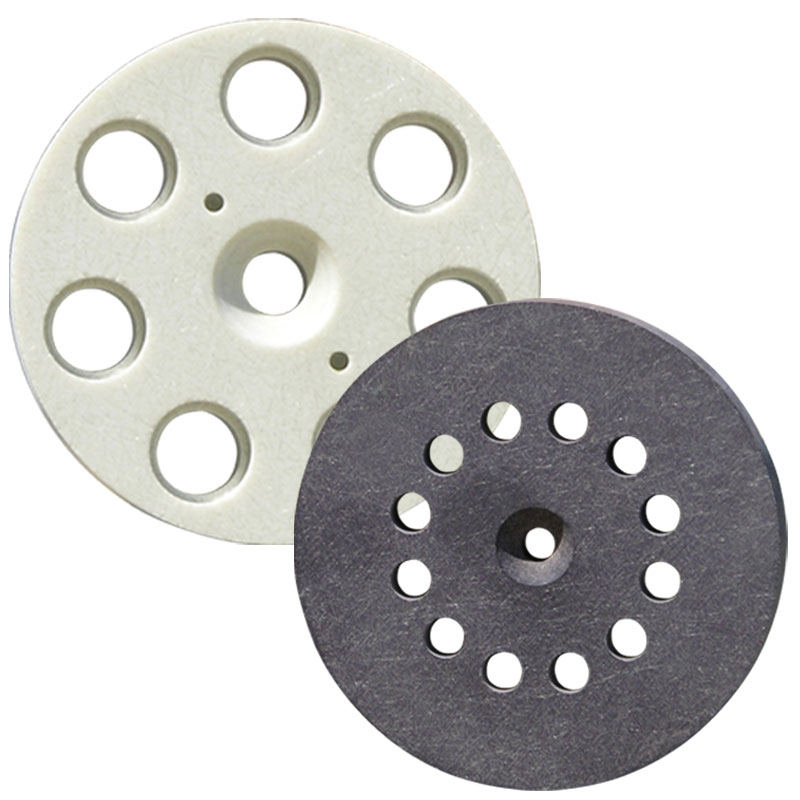
Blow molding is employed to create hollow plastic products, such as bottles and containers. The process involves inflating a hot, hollow tube of plastic within a mold to achieve the desired shape. This method is cost-effective for producing large quantities of lightweight, hollow objects.
III. Applications of Plastic Fabrication:
3.1 Automotive Industry:
Plastic fabrication plays a significant role in the automotive sector, contributing to the production of lightweight components that enhance fuel efficiency. From interior trim components to exterior body panels, plastics are widely used for their durability, versatility, and design flexibility.
3.2 Packaging:
The packaging industry heavily relies on plastic fabrication for creating containers, bottles, and packaging materials. Plastics offer a lightweight and cost-effective solution for protecting and preserving a wide range of products, contributing to the convenience and safety of consumers.
3.3 Medical Devices:
In the medical field, plastic fabrication is instrumental in producing a variety of devices, equipment, and components. Medical-grade plastics ensure compliance with stringent safety and sterilization standards, making them suitable for applications such as medical implants, diagnostic equipment, and packaging for pharmaceuticals.
3.4 Consumer Goods:
Countless consumer goods are manufactured using plastic fabrication processes. Items such as household appliances, electronics, toys, and furniture often incorporate plastic components due to their durability, aesthetic appeal, and cost-effectiveness.
3.5 Construction and Building Materials:
Plastics are increasingly used in construction for their versatility and durability. Plastic fabrication contributes to the production of pipes, insulation materials, roofing, and other components that meet specific performance requirements while offering longevity and ease of installation.
IV. Environmental Considerations:
4.1 Recycling Challenges:
While plastic fabrication has revolutionized manufacturing processes, the environmental impact of plastic waste has become a significant concern. Many plastics are non-biodegradable, leading to challenges in disposal and contributing to pollution. Recycling plastic materials is crucial to mitigate these environmental issues, but the efficiency of plastic recycling varies depending on the type of plastic and the recycling infrastructure in place.
4.2 Sustainable Practices:
The plastics industry is actively exploring sustainable practices to address environmental concerns. This includes the development of biodegradable plastics, the use of recycled materials in fabrication processes, and the adoption of eco-friendly production methods. Sustainable plastic fabrication practices aim to reduce the environmental footprint of plastic products and promote circular economy principles.
4.3 Lifecycle Analysis:
Assessing the environmental impact of plastic products involves conducting a lifecycle analysis that considers the entire lifespan of the material. This includes raw material extraction, manufacturing processes, product use, and end-of-life disposal. By understanding the complete lifecycle, manufacturers can identify areas for improvement in terms of sustainability.
V. Plastic Machining
Plastic machining is a precise and versatile manufacturing process that involves the removal of material from plastic workpieces to achieve desired shapes, dimensions, and surface finishes. This subtractive manufacturing method is commonly used for producing intricate components, prototypes, and custom-designed parts across various industries. Plastic machining encompasses several techniques, each suited to specific applications and requirements.

One of the primary methods used in plastic machining is CNC (Computer Numerical Control) machining. CNC machining involves the use of computer-controlled tools, such as routers, mills, or lathes, to precisely cut, mill, or turn plastic materials into the desired shapes. The process begins with a digital design or CAD (Computer-Aided Design) model, which is then translated into machine code to guide the CNC equipment. This level of automation allows for high precision and repeatability in the manufacturing process.
The choice of plastic material for machining depends on the intended application and the properties required for the final product. Commonly machined plastics include acrylic, polycarbonate, polyethylene, polypropylene, PVC, and others. Each type of plastic offers specific advantages in terms of mechanical properties, chemical resistance, and suitability for different machining processes.
Plastic fabrication is a dynamic and essential component of modern manufacturing, enabling the creation of a vast array of products that touch every aspect of our daily lives. The versatility, precision, and scalability of plastic fabrication processes contribute to its widespread adoption in various industries. As we navigate the challenges posed by plastic waste, the industry is actively exploring sustainable practices and innovations to minimize environmental impact. Understanding the processes, applications, and environmental considerations associated with plastic fabrication is crucial for promoting responsible and informed decision-making in the ongoing evolution of this vital manufacturing method.