ABS (Acrylonitrile Butadiene Styrene) and Delrin (a trade name for acetal homopolymer) are two widely used engineering plastics, each offering a unique set of advantages depending on the application. While both are valued for their durability, versatility, and machinability, they perform differently under various conditions. Choosing between them depends on factors such as performance requirements, environmental exposure, and cost considerations.
When selecting the right material for your plastic machining needs, and ABS offers very good machinability and Delrin offers excellent machinability, solid mechanical performance, and unique advantages depending on your application. But when it comes to Delrin vs ABS, how do you decide?
Let’s break down the differences between these two engineering plastics to help you choose the best one for your next part or product.
Delrin vs. ABS
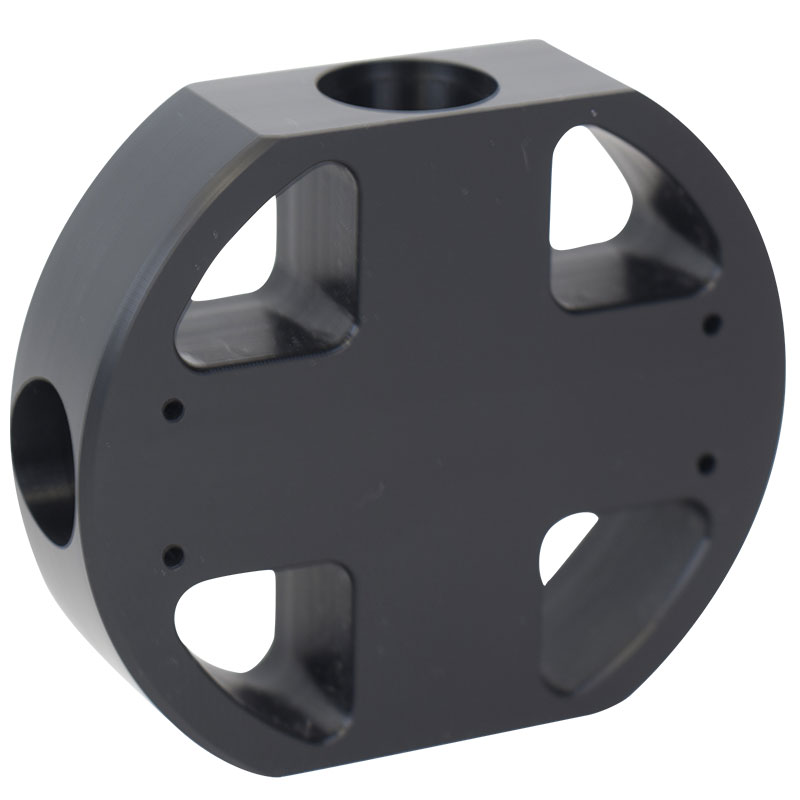

What is Delrin?
Delrin® is a brand name for acetal homopolymer (also known as Polyoxymethylene or POM). Known for its exceptional strength, stiffness, dimensional stability, and low friction, Delrin is often used in place of metal in precision parts. Its excellent moisture and chemical resistance make it ideal for applications in wet or corrosive environments.
Key Benefits of Delrin:
- Tensile Strength: 6,000 – 22,000 psi
- Impact Strength: .90 to 1.5 ft-lb/in.
- Heat Deflection: 26.7° – 149.4°C
- Low coefficient of friction
- Excellent wear resistance
- Great machinability with standard CNC machining tools
What is ABS?
ABS (Acrylonitrile Butadiene Styrene) is a cost-effective, general-purpose thermoplastic widely used in injection molding and prototyping. It’s favored for its dimensional stability, impact resistance, and ease of machining. ABS also offers flexibility in design, with color customization and excellent surface finishing options like painting or plating.
Key Benefits of ABS:
- Tensile strength: 5,000 to 12,000 psi
- Strong impact resistance
- Heat resistance 80°C
- Scratch resistance
- Chemical resistance to acids, alkalis, and oils
- Lower cost than Delrin
- Excellent for mass production
- Good machinability
- Recyclable
Delrin vs. ABS Properties
Property | Delrin | ABS |
---|---|---|
Tensile Strength | High | Moderate |
Impact Resistance | High | High |
Heat Resistance | Up to 100°C | Up to 80°C |
Dimensional Stability | Excellent | Good |
Machinability | Excellent | Excellent |
Surface Finish Options | Limited | Extensive (paint, plating) |
Best Applications for Delrin
Delrin is ideal for high-performance applications that require strength, stability, and precision. Because of its excellent mechanical properties, it is commonly used in:
- Gears and bearings – for low friction and quiet operation
- Fuel system components – especially in automotive applications
- Locking mechanisms – where strength and durability are key
- Medical devices – due to its chemical resistance and stability
- Structural automotive parts – to endure vibration and wear
- Moving assemblies – thanks to its smooth surface finish and low friction
- Marine and outdoor applications – because of its resistance to moisture and chemicals
Best Applications for ABS
ABS is a go-to material when cost, versatility, and visual appearance are priorities. Its wide usage spans both industrial and consumer products, such as:
- Consumer electronics housings – laptops, gaming consoles, and remote controls
- Automotive interior parts – dashboards, trim pieces, and vents
- Protective equipment – including helmets and pads
- Toys and recreational items – like LEGO® bricks and durable playsets
- Prototyping and low-volume production – due to ease of molding and machining
- Instrument enclosures – especially where appearance and custom coloring matter
- Products that need post-processing such as painting, plating, or adding graphic finishes
Which One Should You Choose?
Both Delrin and ABS are excellent plastics—but for very different reasons. Delrin shines in high-performance, precision-machined parts where strength, stiffness, and resistance to wear and chemicals are essential. ABS stands out for cost-effectiveness, design flexibility, and ease of prototyping or molding.
Not sure which one is right for you? Talk to the experts at Jaco Products. Our team can help you select the best material for your project, optimize it for machining or molding, and deliver parts that meet your exact requirements.