What is Ultem?
Ultem is a high-performance thermoplastic material known for its exceptional strength, heat resistance, and chemical resistance properties. Developed by SABIC Innovative Plastics (formerly GE Plastics) in the early 1980s, Ultem has gained widespread recognition and adoption across various industries for its versatility and superior performance in demanding applications. In this comprehensive guide, we explore the characteristics, applications, manufacturing process, benefits, and considerations of Ultem, shedding light on why it has become a material of choice for engineers, designers, and manufacturers worldwide.
Characteristics of Ultem
Ultem is a polyetherimide (PEI) resin characterized by its unique combination of properties that set it apart from conventional thermoplastics. One of Ultem’s key attributes is its exceptional mechanical strength, making it highly resistant to deformation and fracture even under high-stress conditions. This inherent strength enables Ultem to withstand heavy loads, impact, and repetitive stress without compromising structural integrity.
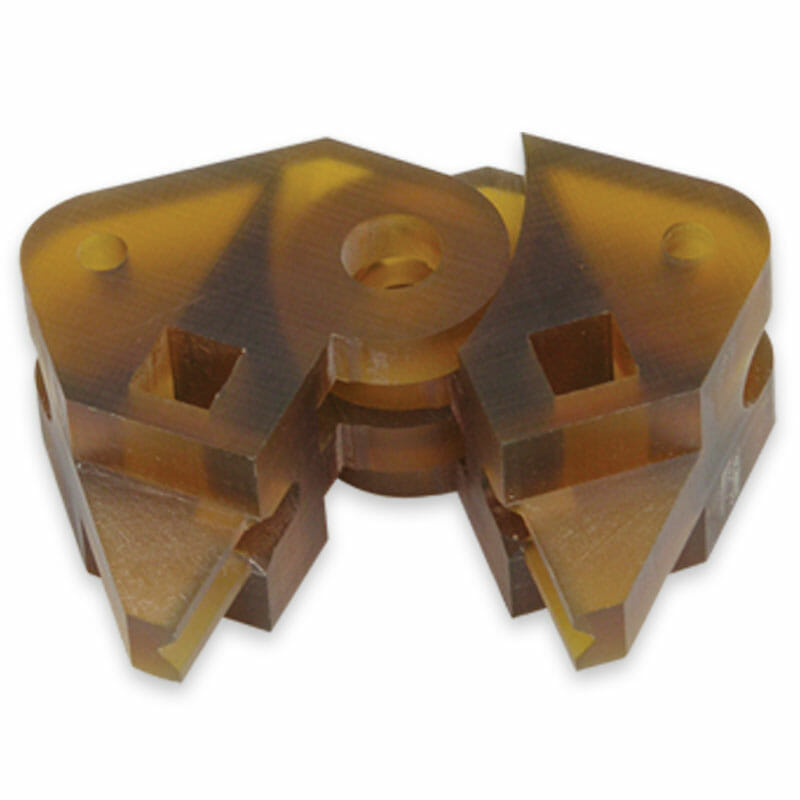
In addition to its mechanical strength, Ultem exhibits outstanding heat resistance, with a continuous-use temperature range spanning from -40°C to 170°C (-40°F to 338°F). This thermal stability allows Ultem to maintain its properties and dimensional stability over a wide temperature range. This makes it suitable for use in applications exposed to extreme heat or thermal cycling.
Furthermore, Ultem possesses excellent chemical resistance, with the ability to withstand exposure to a wide range of chemicals, solvents, and cleaning agents without degradation or corrosion. This chemical inertness makes Ultem ideal for applications requiring resistance to harsh environments or chemical exposure, such as in the aerospace, automotive, and semiconductor industries.
Ultem is also inherently flame-retardant, meeting various flammability standards such as UL94 V0, making it suitable for use in applications where fire safety is a concern. Additionally, Ultem exhibits low smoke and toxicity emissions when exposed to fire, further enhancing its suitability for use in enclosed spaces or critical applications.
Applications of Ultem
The exceptional properties of Ultem make it a preferred material choice for a wide range of applications across diverse industries. In the aerospace sector, Ultem is used in aircraft interiors, structural components, and engine components due to its lightweight, high strength-to-weight ratio, and flame-retardant properties. In the automotive industry, Ultem finds application in under-the-hood components, lighting systems, electrical connectors, and interior trim components, where heat resistance, dimensional stability, and durability are critical requirements.
In the medical device industry, Ultem is utilized in surgical instruments, diagnostic equipment, and medical device housings due to its biocompatibility, sterilizability, and chemical resistance. In the semiconductor and electronics industries, Ultem is employed in wafer handling, chip manufacturing, and electronic device housings due to its high dielectric strength, thermal stability, and dimensional precision.
Ultem is also widely used in consumer electronics, industrial machinery, food processing equipment, and telecommunications applications, where its combination of strength, heat resistance, chemical resistance, and flame retardancy provides unique advantages.
Manufacturing Process of Ultem
Ultem is typically produced through a process called injection molding, where molten Ultem resin is injected into a mold cavity under high pressure and temperature. The mold is then cooled, allowing the Ultem resin to solidify and take the shape of the mold cavity. This injection molding process enables the production of complex shapes and intricate geometries with tight tolerances, making Ultem suitable for a wide range of applications.
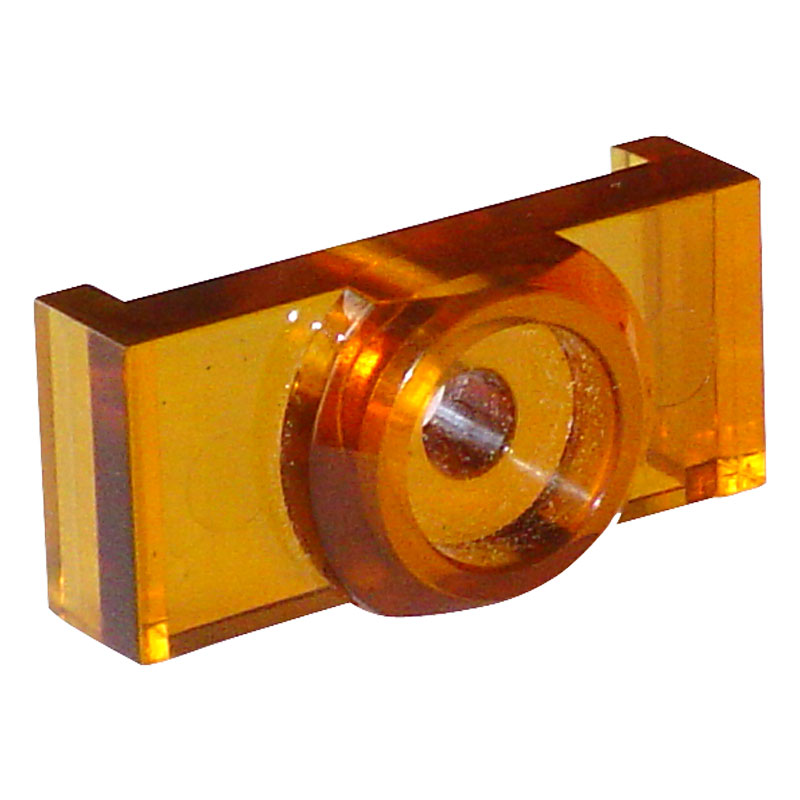
Benefits of Ultem
The use of Ultem offers several benefits to manufacturers, designers, and end-users. Its exceptional strength and durability enable the production of lightweight yet robust components, reducing material usage and assembly costs while improving product performance and longevity. Ultem’s high heat resistance allows for the creation of components that can withstand elevated temperatures without deformation or degradation, expanding the range of operating conditions for various applications.
Moreover, Ultem’s chemical resistance and flame-retardant properties enhance product reliability and safety, reducing the risk of material degradation, failure, or fire hazards in critical applications. Additionally, Ultem’s biocompatibility and sterilizability make it suitable for use in medical and pharmaceutical applications, where strict regulatory requirements and patient safety considerations are paramount.
Considerations When Using Ultem
While Ultem offers numerous advantages, there are some considerations to keep in mind when selecting and using this material. Ultem’s high-performance properties come at a premium cost compared to conventional thermoplastics, which may impact the overall project budget. Additionally, the high processing temperatures required for molding Ultem resin may necessitate specialized equipment and tooling, increasing manufacturing complexity and investment requirements.
Furthermore, Ultem’s high melt viscosity and crystallinity can pose challenges during processing, such as flow limitations, warpage, or sink marks, requiring careful design and processing optimization to achieve desired results. It’s also important to consider Ultem’s compatibility with specific chemicals, sterilization methods, and environmental conditions to ensure long-term performance and reliability in intended applications.
Furthermore, Ultem’s high melt viscosity and crystallinity can pose challenges during processing, such as flow limitations, warpage, or sink marks, requiring careful design and processing optimization to achieve desired results. It’s also important to consider Ultem’s compatibility with specific chemicals, sterilization methods, and environmental conditions to ensure long-term performance and reliability in intended applications.
While Ultem offers numerous advantages in various applications, it also comes with certain drawbacks that users should consider.
Cost: One of the primary drawbacks of Ultem is its relatively high cost compared to other thermoplastics. The manufacturing process for Ultem involves specialized equipment and precise control over processing parameters, leading to higher production costs. This elevated cost can be a significant factor for budget-conscious projects, especially when considering large-scale production or applications that require extensive material usage.
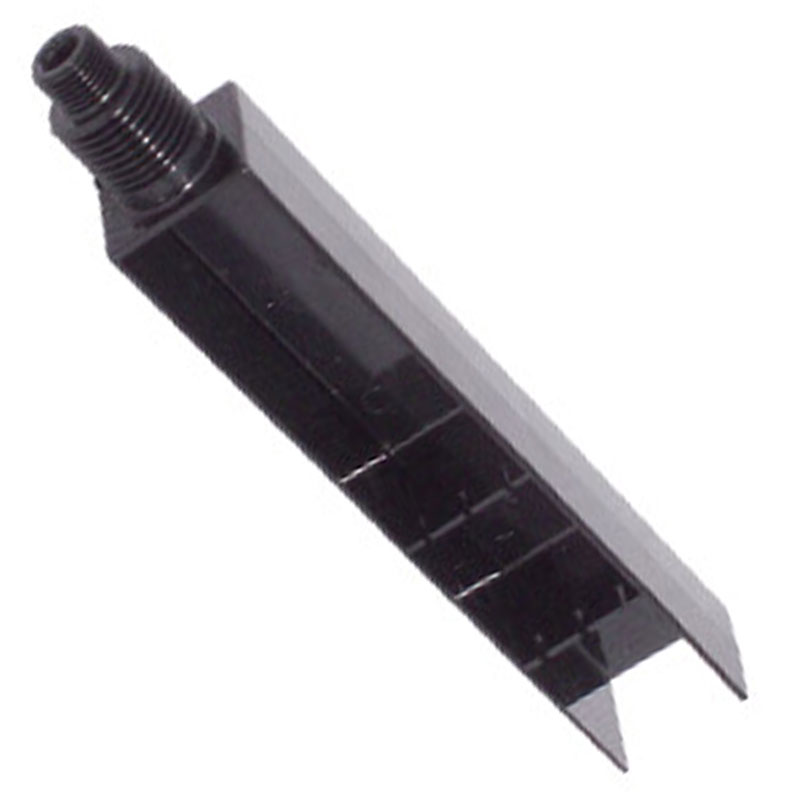
Processing Challenges: Ultem’s high-temperature resistance presents challenges during the processing and fabrication stages. The material has a high melting point, typically around 217-225°C (422-437°F), which requires specialized equipment capable of reaching and maintaining such temperatures. Additionally, Ultem’s high melt viscosity can result in challenges during injection molding, extrusion, or other processing methods, potentially leading to longer cycle times, increased energy consumption, and higher production costs.
Limited Color Options: Ultem is available in a limited range of colors compared to other thermoplastics. While some grades of Ultem may offer options for custom colors, the standard offerings are often limited to natural or amber hues. This limitation may pose challenges for applications that require specific color requirements or aesthetic considerations.
Moisture Absorption: Ultem has a tendency to absorb moisture from the surrounding environment, which can affect its mechanical properties and dimensional stability. Moisture absorption can lead to changes in material properties, such as reduced tensile strength, increased elongation, and dimensional variations, particularly in applications exposed to high humidity or moisture-rich environments. Proper storage and handling practices are essential to mitigate the effects of moisture absorption in Ultem components.
Chemical Sensitivity: While Ultem exhibits excellent chemical resistance to a wide range of substances, it may be susceptible to degradation or damage when exposed to certain chemicals or solvents. Specific grades of Ultem may offer enhanced chemical resistance compared to others. However, users should carefully consider the compatibility of Ultem with the intended environment or application. Exposure to incompatible chemicals can lead to deterioration of material properties, surface degradation, or even structural failure over time.
Machining Challenges: Ultem’s high strength and hardness can pose challenges during machining operations. The material’s abrasion resistance and low thermal conductivity can result in accelerated tool wear, increased machining forces, and difficulty in achieving precise dimensional tolerances. Specialized cutting tools, cooling strategies, and machining techniques may be required to effectively machine Ultem components while maintaining quality and efficiency.
Conclusion
Ultem stands out as a high-performance thermoplastic material renowned for its exceptional strength, heat resistance, chemical resistance, and flame retardancy properties. With its versatility, reliability, and suitability for demanding applications across industries, Ultem has become a material of choice for engineers, designers, and manufacturers seeking to optimize product performance, safety, and durability. By understanding the characteristics, applications, manufacturing process, benefits, considerations, and limitations of Ultem, businesses can leverage its unique properties to innovate, enhance competitiveness, and meet the evolving needs of their markets.