Ultem vs G10 Overview
Ultem and G10 are two highly valued materials in the precision machining industry, each known for their distinct properties and advantages. Ultem, a polyetherimide (PEI) thermoplastic, is prized for its high strength, excellent thermal resistance, and ease of machining, making it ideal for complex components that must withstand extreme conditions. G10, on the other hand, is a fiberglass epoxy laminate known for its outstanding mechanical strength and dimensional stability. It is commonly used for applications where toughness and durability are critical. Understanding these materials’ properties and applications is key to choosing the right one for your project.
Ultem: Key Properties and Applications
Ultem is a high-performance thermoplastic that excels in environments requiring both strength and heat resistance. Known for its ability to withstand temperatures up to 340°F (170°C), Ultem maintains its structural integrity under demanding conditions, making it a preferred choice in industries like aerospace and automotive. It offers excellent chemical resistance, reducing the risk of material degradation when exposed to harsh substances. Additionally, Ultem’s machinability allows for precise fabrication of intricate parts, ensuring accuracy in complex assemblies.
In machining, Ultem is often used for components such as electrical insulators, medical devices, and structural elements that require both rigidity and lightweight properties. Its versatility extends to applications where flame retardancy is important, as Ultem meets UL94-V0 standards, ensuring safety in high-risk environments.
G10: Key Properties and Applications
G10 is a fiberglass epoxy laminate renowned for its toughness and durability. It is created by layering fiberglass cloth with epoxy resin, resulting in a material that offers exceptional mechanical strength and dimensional stability. Unlike Ultem, G10 is known for its resistance to moisture, making it an excellent choice for environments where exposure to humidity or water is a concern. This property, along with its high tensile strength, ensures that G10 components maintain their integrity even under heavy loads or impact.
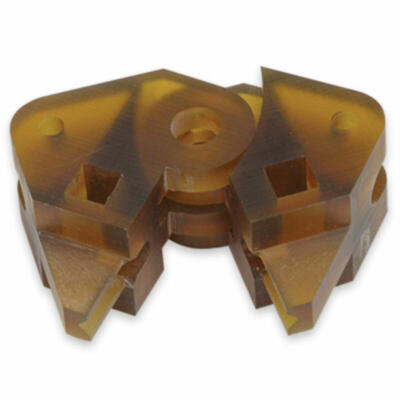
In machining applications, G10 is commonly used for electrical insulators, structural supports, and components in industrial and marine settings. Its lightweight yet strong nature makes it suitable for parts that need to be both durable and easy to handle. Additionally, G10’s ability to be precisely machined into complex shapes allows for versatility in design, accommodating various custom parts and prototypes.
Ultem vs G10: How to Choose the Right Material
When deciding between Ultem and G10 for your machining project, it’s essential to evaluate your specific requirements. If your application demands high thermal resistance, rigidity, and chemical resilience, Ultem is often the superior choice. It’s particularly effective for components in high-heat or chemically harsh environments, such as aerospace parts or electrical insulators that need to maintain performance under stress.
On the other hand, G10 is ideal for projects that prioritize moisture resistance, toughness, and durability. Its ability to withstand impact and maintain structural integrity in humid or wet conditions makes it a go-to option for marine, industrial, and outdoor applications. Additionally, G10’s strong mechanical properties and lightweight nature make it suitable for components that must handle heavy loads or repeated impact without compromising on stability.
Ultimately, the choice between Ultem and G10 depends on the specific demands of your project, whether that involves temperature, chemical exposure, moisture, or mechanical strength. Consulting with experts like Jaco Products can help ensure you select the material best suited for your needs.