PEEK vs Delrin: Which Material is Right for Your Project?
Choosing between high-performance plastics like PEEK and Delrin requires understanding their key differences. Each excels in different applications due to its distinct properties. Delrin, a low-friction, high-strength acetal homopolymer, is valued for its durability and cost-effectiveness, making it a staple in automotive, medical, and industrial applications.
PEEK is known for its extreme heat and chemical resistance, making it essential in aerospace, medical implants, and demanding industrial applications.
Both materials are lightweight and machinable but serve different roles. Delrin is affordable and ideal for wear-resistant parts, but it lacks PEEK’s extreme heat and chemical resistance. Although PEEK is significantly more expensive, it’s indispensable in demanding environments where heat, chemicals, or mechanical stress would break down most other plastics.
So, how do you decide between PEEK vs Delrin? This guide will compare their key properties, benefits, applications, and cost differences—all in a clear, side-by-side format to help you choose the best material for your needs.
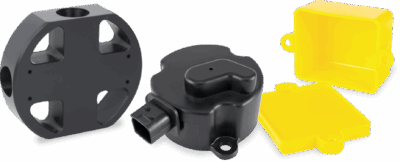
Delrin
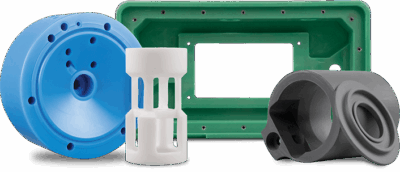
PEEK
Delrin vs PEEK: Side-by-Side Comparison
Property | Delrin (Acetal Homopolymer) | PEEK (Polyether Ether Ketone) |
---|---|---|
Density (g/cm³) | 1.41 | 1.33 |
Melting Point (°C) | 175 | 343 |
Tensile Strength (MPa) | 69-80 | 100 – 115 |
Modulus (GPa) | 2.8 – 3.5 | 3.6 |
Water Absorption (%) | 0.3 | 0.05 – 0.2 |
Chemical Resistance | Good (limited acids) | Excellent |
Heat Deflection (°C) | 120 – 170 | 160 – 180 |
Friction Coefficient | Low (0.2 – 0.3) | Very Low (0.1 – 0.2) |
UV Resistance | Low | Moderate |
Cost ($/kg) | $5 – $15 | $90 – $400 |
Advantages & Disadvantages: Delrin vs PEEK
Delrin offers durability, dimensional stability, and low friction, making it ideal for automotive, industrial, and mechanical components. Its self-lubricating properties minimize wear, enhancing performance in gears, bearings, and moving parts. However, Delrin is not resistant to strong acids, alkalis, or UV exposure, which limits its use in chemically aggressive or outdoor environments.
PEEK, on the other hand, is a high-performance plastic with superior heat and chemical resistance. It can withstand temperatures up to 260°C while maintaining its mechanical properties, making it indispensable in aerospace, medical implants, and oil & gas applications. Additionally, PEEK’s biocompatibility and fatigue resistance make it a preferred choice for medical implants and other demanding applications. However, its high cost makes it impractical for standard applications where Delrin or other plastics suffice.
Applications: Where Are Delrin and PEEK Used?
Application | Delrin (Best For…) | PEEK (Best For…) |
---|---|---|
Automotive | Seatbelt bucklers, gears, fuel system parts | High-temp engine seals, under-hood parts |
Medical Devices | Handles for surgical tools, non-implant parts | Spinal implants, orthopedic screws |
Aerospace | Structural support brackets | Lightweight, high-heat-resistant components |
Industrial Machinery | Conveyor belts, rollers, electrical housings | Corrosion-resistant electrical connectors |
Electronics | Insulating components, switch housings | Semiconductor and high-voltage insulators |
Which Material Should You Choose?
For durable, low-friction mechanical parts, Delrin is a practical, cost-effective choice. It’s lightweight, low-friction, and easy to machine, but lacks chemical and heat resistance.
PEEK is best for high-temperature, chemically aggressive, or medical applications. It offers superior durability, biocompatibility, and fatigue resistance, but comes at a higher cost.
- Delrin excels in budget-friendly, durable, and low-friction applications.
- PEEK is essential for extreme heat, chemical stability, and high-performance needs.
Both PEEK and Delrin are exceptional engineering plastics, but they serve very different purposes. If you’re looking for an affordable, strong, and wear-resistant material for industrial applications, Delrin is the best choice. However, if your project demands extreme heat resistance, chemical durability, and biocompatibility, PEEK is the superior option—even at a premium cost.
Still unsure which material is right for your project? Contact Jaco Products for expert guidance and custom machining solutions tailored to your needs.