When selecting materials for CNC plastic machining, Delrin (POM) and Teflon (PTFE) often come up as two of the most widely used options. Both are high-performance engineering plastics known for their unique properties, but they serve different purposes across various industries.
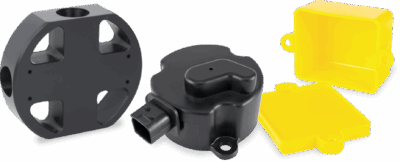
Delrin
Whether you’re designing gears, bushings, seals, or bearings, understanding how these materials compare can help you choose the right one for your application.
Delrin is a rigid, high-strength thermoplastic with excellent wear resistance and dimensional stability, making it ideal for precision mechanical components. In contrast, Teflon is valued for its ultra-low friction, nonstick properties, and chemical resistance, making it the go-to material for applications requiring minimal friction or exposure to harsh environments.
Teflon vs. Delrin – Properties and Key Differences
Both Delrin (POM) and Teflon (PTFE) are widely used engineering plastics, but they have distinct properties that make them suitable for different applications. Understanding their differences in strength, friction, temperature resistance, and chemical stability is essential when selecting the right material for CNC machining.
Material Overview
Delrin (Polyoxymethylene – POM): A high-strength, rigid thermoplastic known for excellent dimensional stability, wear resistance, and low friction. Commonly used in precision components such as gears, bushings, and mechanical parts.
Teflon (Polytetrafluoroethylene – PTFE): A fluoropolymer known for exceptional nonstick properties, low friction, and chemical resistance. Often used in seals, gaskets, and industrial applications requiring minimal friction.
Comparison Table: Delrin vs. Teflon
Property | Delrin (POM) | Teflon (PTFE) |
---|---|---|
Tensile Strength (MPa) | 50–80 | 20–30 |
Friction Coefficient | 0.2 – 0.4 | 0.04 – 0.06 |
Heat Resistance (°C) | Up to 100°C | Up to 260°C |
Chemical Resistance | Moderate | Excellent |
Water Absorption (%) | 0.2 – 0.9 | < 0.01 |
Machinability | Excellent | Moderate |
Key Differences Explained
Strength & Durability: Delrin is significantly stronger and stiffer than Teflon, making it ideal for structural components and mechanical parts.
Friction & Wear Resistance: Teflon has a much lower friction coefficient, meaning it reduces drag and wear more effectively in applications such as bearings and slide plates.
Temperature Resistance: Teflon withstands much higher temperatures (up to 260°C), while Delrin starts to lose stability above 100°C.
Chemical Resistance: Teflon offers near-universal chemical resistance, whereas Delrin is sensitive to strong acids and bases.
Delrin vs. Teflon Friction – Which One is Better?
Friction plays a crucial role in determining how materials perform in moving components such as bearings, bushings, gears, and seals. Both Delrin and Teflon offer low friction, but they behave differently in terms of wear resistance and surface interaction.
Friction Coefficients of Delrin vs. Teflon
- Delrin (POM): 0.2 – 0.4 (static & dynamic)
- Teflon (PTFE): 0.04 – 0.06 (static & dynamic)
Friction Performance in Applications
Teflon (PTFE) is one of the slickest materials available, making it the superior choice for applications where low friction is essential. It reduces wear and energy consumption in components like gaskets, seals, and non-stick coatings.
Delrin (POM) has a low friction coefficient compared to many plastics and metals but is not as slippery as Teflon. However, it excels in load-bearing applications where strength, durability, and impact resistance are needed.
Which One Should You Choose?
- Use Teflon for low-friction applications like slide rails, lubrication-free bearings, and chemical-resistant seals.
- Use Delrin where friction matters but strength is also critical, such as precision gears, wear-resistant rollers, and automotive components.
Best Applications for Delrin and Teflon
Both Delrin (POM) and Teflon (PTFE) are widely used in industrial, automotive, and consumer applications, but their strengths make them better suited for different roles.
Common Uses for Delrin
Delrin is preferred when strength, stiffness, and wear resistance are needed:
- Gears & Bearings – Strong enough to replace metal components in machinery.
- Bushings & Rollers – Provides smooth motion while resisting wear.
- Automotive Components – Used in fuel system parts, seatbelt components, and mechanical linkages.
- Electrical Insulation – Stable and durable for switch housings and insulators.
- Precision Parts – Excellent machinability makes it ideal for tight-tolerance components.
Common Uses for Teflon
Teflon is chosen for low friction, chemical resistance, and high-temperature stability:
- Seals & Gaskets – Resistant to extreme chemicals and temperatures.
- Nonstick Applications – Used in cookware, food processing, and industrial coatings.
- Bearings & Slide Plates – Ultra-low friction for smooth motion with minimal wear.
- Medical & Pharmaceutical Equipment – Chemically inert and biocompatible for medical-grade tubing and components.
- Aerospace & Industrial Applications – Withstands extreme heat and friction in high-performance systems.
Choosing the Right Material for Your Application
Selecting between Delrin (POM) and Teflon (PTFE) comes down to understanding the demands of your specific application. While both materials offer unique advantages, their performance differs significantly in terms of strength, friction, temperature resistance, and chemical stability.
Choose Delrin if you need:
- High strength and stiffness for mechanical components
- Durability and wear resistance for gears, bearings, or bushings
- Tight machining tolerances for precision applications
Choose Teflon if you need:
- Low friction and nonstick properties for sliding components
- Chemical and heat resistance in extreme environments
- Electrical insulation for high-performance applications
If you’re still unsure which material is best for your project, Jaco Products specializes in custom machining solutions for both Delrin and Teflon. Their expertise ensures you get the right material for optimal performance and longevity. Contact Jaco Products today to discuss your application needs!